- Home
- Technologies
- Tunnelling
Bored underground works
Metrostav owns complex assemblies of full-profile boring machines (TBMs), enabling the efficient implementation of long tunnels by mechanically boring a circular cross-section of the required size into the rock mass with continuous securing of the cut against flooding with a definitive lining.
For the construction of shorter tunnels or in the case of difficult geological conditions, it also uses the conventional tunnelling method"New Austrian Tunnelling Method" (NATM), which is characterised by its organisation of the work, including the definitive method, or the Drill & Blast method.
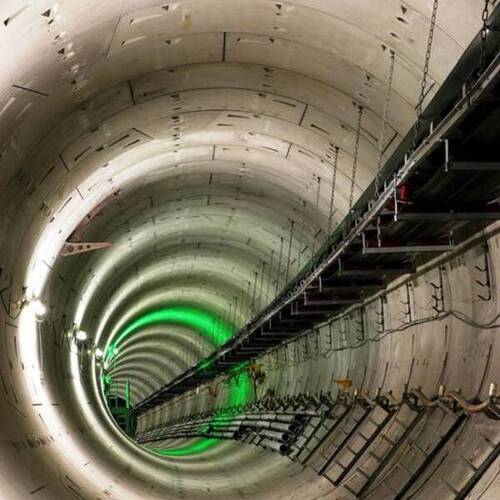
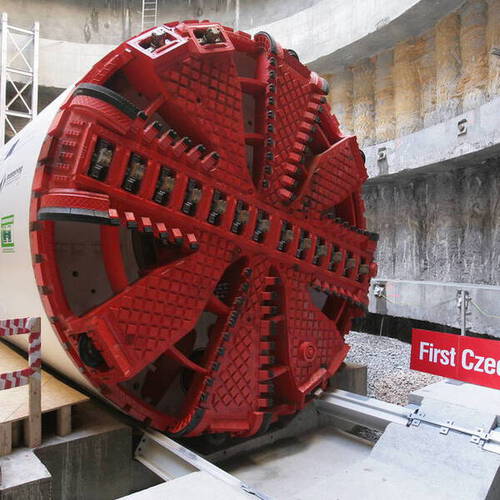
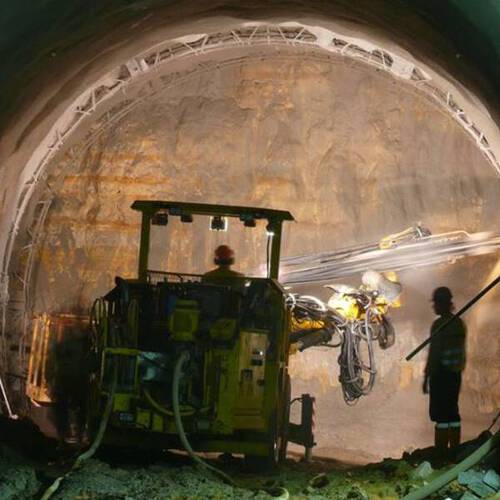
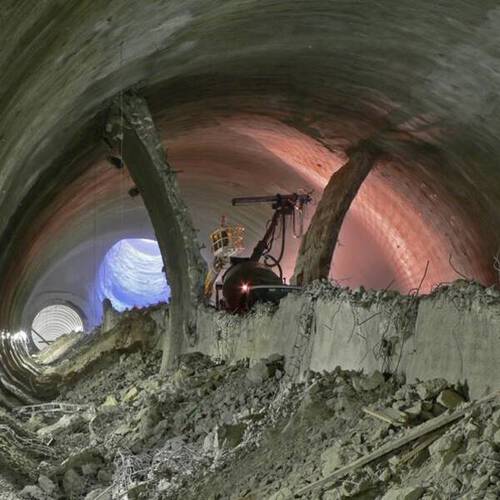
New Austrian Tunneling Method – NATM
The NATM is a tunnelling method that consciously and purposefully uses the load-bearing properties of the rock mass in order to optimise the process of boring and securing the cut and minimise the associated economic costs. In tunnel construction using the NATM, the stability of the excavation is usually ensured by the primary lining and the final tunnel tube structure (secondary lining) is built only after the stress-strain state in the vicinity of the excavation has stabilized.
The main structural elements of the primary lining are shotcrete and the anchoring system. An integral part of the NATM is geotechnical monitoring based primarily on measuring the deformation of the tunnel excavation. From the geotechnical point of view, the NATM is thus classified as a group of observational methods in which the construction progress is continuously monitoredand the method of excavation and securing the excavation with primary lining are adjusted according to the nature of the excavation and behaviour of the rock mass.
Boring with full-profile tunnelling machines
Full-profile tunnelling machines are powerful mechanisms that can be used to continuously separate the rock throughout the tunnel face without the use of blasting and at the same time build the tunnel lining almost continuously. In fact, even tunnelling machines or rather the pistons of the radial presses, that disconnect the rock after the shots given by the maximum possible extension of the thrust axial presses and after the extension is exhausted, must be moved. At this stage, the separation of the rock in the face is interrupted.
In hard rock, open tunnelling machines are used with radial pressure plates (grippers) that stabilize the machine and provide support for the machine to press into the face via axial presses. If necessary, the cut is secured with bolt reinforcement in combination with shotcrete. In low-strength, faulty and semi-hard rock or soil, tunnelling machines equipped with a protective shield are used, which ensures the stability of the excavation during boring and enables the safe execution of the final tunnel reinforcement. The cutting is ensured by lining made of segments stacked into individual lining rings. At present, precast reinforced concrete partsare mainly used, but wire concrete partsare also increasingly being used. Soft rocks and soils do not allow the use of grippers, therefore the machine is supported by axial presses on the last ring of the segmental lining being built.
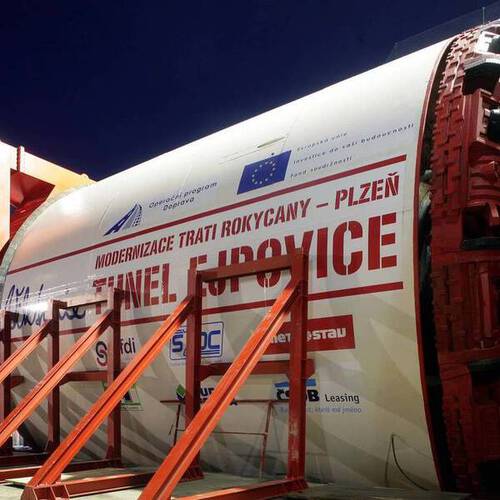
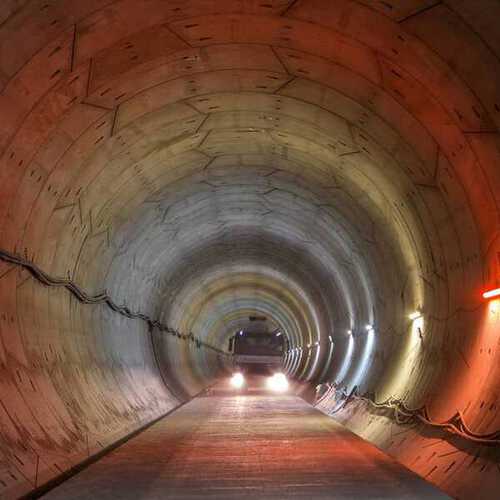

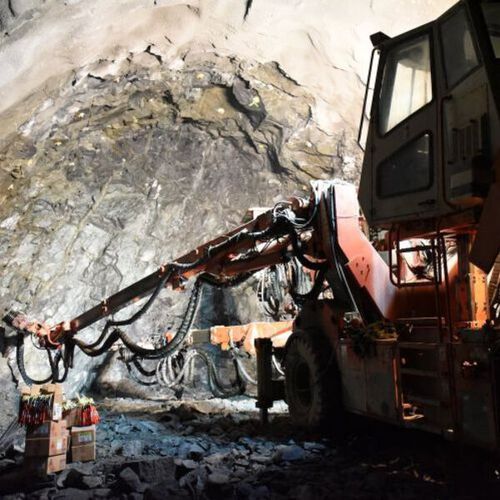
Drill & Blast method of boring
This method of tunnelling is based on the principles of the Norwegian tunnelling method, which has proven to be very efficient and successful over the last forty years. The boring is usually carried out using blasting, and in exceptional cases also with machine separation. Convergence measurements are not systematic, they take place mainly in fault zones.
Another fundamental aspect of the Drill & Blast method is the use of bolts and shotcrete with dispersed reinforcement (steel wires or polypropylene fibres) as temporary reinforcement. Thetemporary reinforcement is not separated from the final lining and forms a single unit. The final reinforcement usually consists of an additional layer of shotcrete and the addition of bolts in a defined grid. The design of the work reinforcement is carried out shot by shot based on the Q-system. The Q index is determined based on an empirical system that uses the RQD index supplemented by five other parameters such as the number of fracture systems, fracture roughness, alteration of discontinuity or fill surfaces, water pressure, and rock mass pressure conditions.
This Technology Has Been Successfully Used in the Following Projects:
See Also Our Other Technologies
Ask us a question
Contact us, we'll be happy to answer